The rapid pace of technological advancement today is nothing short of amazing. Amidst this fast-paced landscape, one constant remains - the role of simulation in driving innovation.
Simulations are pivotal in design and development across various industries.
Yet, there exists an unexploited capacity for advanced simulation, especially within industries like Microelectromechanical Systems (MEMS).
In the MEMS sector, simulations typically find limited use, predominantly in the early phase of design.
Consequently, this often leads to missed opportunities for optimization and thorough design validation in the later stages of product development.
But what if we could overcome these limitations? What if we had the means to utilize simulation fully in MEMS design?
In this blog post, we explore this possibility, underscoring the need for robust simulation tools that cater specifically to the unique demands of the MEMS industry and introduce Quanscient Allsolve - our solution to this industry-wide need.
The role of FEM-based simulation in MEMS device design
The Finite Element Method (FEM), a powerful physics-based simulation tool, plays a critical role in the design of new MEMS devices.
This numerical approach for solving problems in engineering and mathematical physics is essential, particularly during the early stages of product design for verifying product specifications.
However, the road can be rocky.
Traditional FEM simulation tools often hit a stumbling block when it comes to computational capacity and flexibility.
They are frequently hampered by limitations on problem size, capability, throughput, and licensing requirements, which can become a bottleneck for design engineers, restricting the extent to which FEM can be utilized.
Despite the valuable insights and precision offered by FEM, many MEMS design teams find themselves unable to fully leverage this powerful tool in the later, and equally critical, stages of the design process.
The inability to make the most of FEM for complex simulations underscores an industry-wide challenge but also opens a gateway of opportunity.
The challenges and opportunities in FEM-based simulations
As we proceed further into the complicated world of MEMS design, the complexity of the devices, coupled with system-level effects such as packaging, come to the forefront.
These challenges require simulation tools that not only handle a diverse range of parameters but can do so quickly to optimize performance.
Enter the Design of Experiments (DoE). An essential method for reducing the number of fabrication runs needed to optimize realistic device performance before launching production tape-outs.
Conducting reliable DoEs, however, isn't a straightforward task. It requires the intense deployment of FEM, unhindered by the conventional constraints on problem size, capability, throughput, hardware, and licensing.
The proposition of a 'restriction-free' simulation environment presents both a challenge and a significant opportunity.
The removal of these traditional barriers allows MEMS design teams to fully exploit the capabilities of FEM-based simulations, leading to more efficient designs and an accelerated design process.
'Production level' simulations: a game changer?
So, what does 'production level' simulation entail, and why is it crucial in the MEMS design landscape?
'Production level' simulation signifies a dramatic shift in the utilization of simulation within the design process.
It involves the deployment of simulation at a 'production level,' enabling the execution of thousands of simulations, thereby allowing for an exhaustive exploration of design space.
Such an approach is especially important in complex systems like MEMS, where every detail can significantly influence the final product's performance and manufacturability.
When unrestricted FEM is combined with reliable DoEs, it morphs into a robust tool capable of addressing even intricate design challenges. This combination assists in navigating the labyrinth of variables, constraints, and trade-offs that MEMS design engineers encounter regularly.
Furthermore, merging statistical techniques such as Monte Carlo analysis with FEM heralds new possibilities. It facilitates predicting critical outcomes like yield, a key consideration in any manufacturing process.
This integration marks a step-change in how FEM is leveraged within the MEMS industry, allowing design teams to extract even greater value from their simulation efforts.
Quanscient Allsolve in reforming simulations in the MEMS Industry
Quanscient Allsolve is our answer to the industry's need for an unrestricted, advanced simulation tool.
Designed specifically with the MEMS industry in mind, Quanscient Allsolve is positioned to redefine how simulations are used in the design process.
Quanscient Allsolve is more than just a tool for the early design phases. Its true value comes to the fore in the later stages of the design process.
Its speed and versatility make it an exceptional asset for running complex, numerous simulations simultaneously, helping engineers navigate the sea of design possibilities efficiently and confidently.
With Quanscient Allsolve, you can optimize your design to be cost-efficient to manufacture, function effectively, and operate reliably in various environments.
It allows for the execution of vast simulations that can verify and fine-tune your design, helping you spot potential issues before they turn into costly problems.
Quanscient Allsolve represents the next step in the evolution of the MEMS industry, promoting innovation and efficiency through advanced simulation capabilities.
It's not just about meeting the demands of today, but facilitating the MEMS industry's future.
Conclusion
The paradigm shift from 'traditional' to 'production level' simulation in the MEMS industry is much more than an upgrade.
By removing traditional barriers of FEM, we stand on the brink of new possibilities and improvements in MEMS design.
Quanscient Allsolve is at the heart of this transformation, equipped to meet the industry's demands today and flexible enough to adapt to the needs of tomorrow. Our solution promises to not just meet the status quo but to elevate it.
Imagine being able to conduct high fidelity DoEs and statistical analyses to improve design parameters like yield. Picture no longer being hindered by problem size, capability, throughput, hardware, and licensing
This is the vision we have turned into a reality with Quanscient Allsolve.
So we leave you with this thought: if you could run more FEM to facilitate these advanced analyses, wouldn't you?
We invite you to explore Quanscient Allsolve and experience firsthand how it can redefine your design process and catalyze innovation in the MEMS industry.
Read more about our MEMS capabilities and book a demo.
Join 1000+ others and start receiving our weekly blog posts to your inbox now
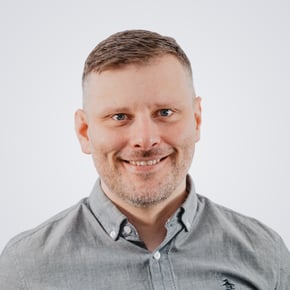