Comprehensive simulation platform for advanced MEMS design
Scalable, high-accuracy MEMS simulations for optimized yield, reliability, and performance.
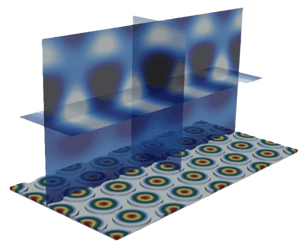
Proxima Fusion
Tampere University
UKAEA
Proxima Fusion
Key advantages in MEMS design
Run thousands of simulations in parallel, explore a wider design space, and optimize device performance without constraints
Estimate manufacturing yield by taking into account real-world conditions and manufacturing constraints
Capture complex interactions between elastic waves, acoustics, and piezoelectric / electrostatic effects
Integrate Allsolve into your workflows and automate custom design processes with the Quanscient API
Trusted by both industry and academia
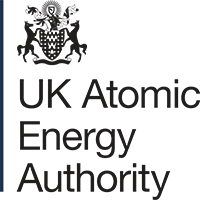

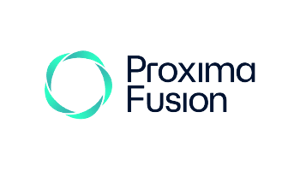
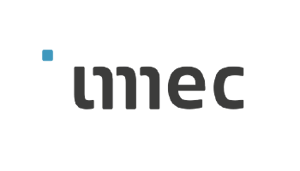
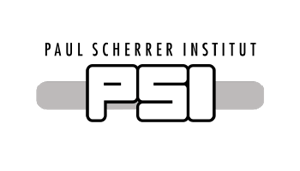
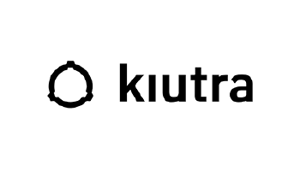
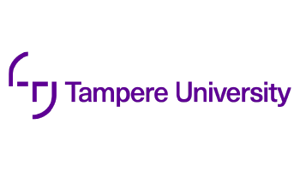
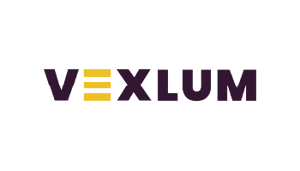
.png?width=300&name=Boston_Scientific_Logo%20(1).png)
Traditional software often requires simplifications, compromises on accuracy, or long runtimes
-
Extensive physical prototyping to validate designs
-
Time-consuming and expensive process
-
Limited computational resources
-
Inability to fully explore all potential design possibilities
Suboptimal designs that fail to maximize yield, reliability, or performance.
-
Complex interactions between multiple physics domains (mechanical, thermal, electrical, fluidic)
-
Struggle to accurately simulate multiphysics interactions
-
Simplified models or separate simulations for each domain
Inaccurate results and potential oversights in the design process.
-
Struggle to create accurate simulation meshes
-
Simplified models that do not fully capture the real-world behavior of the device
Less accurate simulation results.
Production-level simulation platform for advanced MEMS design
Quanscient Allsolve was developed for accelerating the design and optimization of high-performance MEMS devices by providing accurate, scalable, and efficient multiphysics simulations. As a production-level tool, Allsolve offers capabilities for running large design of experiments for product optimization in later design stages, as well as earlier exploratory simulations.
Accelerated design cycles and reduced reliance on physical prototypes
- Powerful solvers and virtually unlimited computational resources
- Test and validate design variations with faster speed and increased accuracy
- Reduce the need for extensive physical prototyping
-> Shortened development timelines and faster time-to-market.
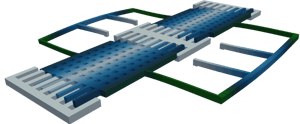
Optimized design exploration
- Access to extensive computational resources and faster simulation times
- Explore a wider range of design possibilities within the same timeframe
- More thorough optimization process
-> Designs that maximize yield, reliability, and performance.
Comprehensive multiphysics simulations
- Accurate and efficient simulation of complex multiphysics interactions through natively coupled multiphysics algorithms
- Eliminate the need for simplified models or separate simulations for each domain
-> More comprehensive and reliable design validation.
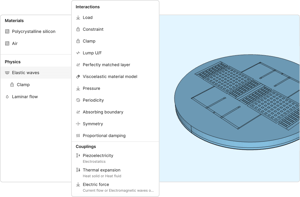
Accurate meshing of complex geometries
- High-quality meshes for even the most intricate geometries
- Accurately capture the real-world behavior of the device
-> More accurate and reliable results
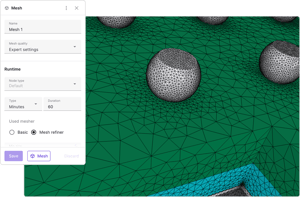
Proven applications
Quanscient Allsolve has been successfully applied to a wide range of ultrasound applications.Medical imaging
PMUTs, CMUTs, Piezocomposites
Fingerprint sensing
PMUTs, CMUTs, Thin-film piezoelectrics
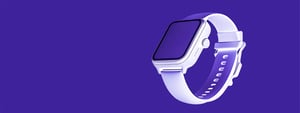
Wearable devices
Gyroscopes, accelerometers
Microvalves
Electrostatic, piezoelectric, thermal microactuators
Underwater sonar
Piezocomposites, Piezo stacks (Tonpilz, Langevin)
Automotive sensing
Parking sensors, passenger occupancy sensing
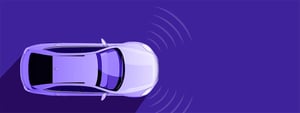
Proven applications
Quanscient Allsolve has been successfully applied to a wide range of applications.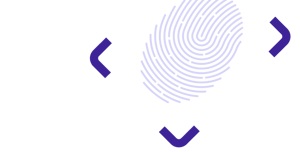
Fingerprint sensing
PMUTs, CMUTs, Thin-film piezoelectrics
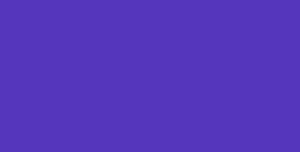
Medical imaging
PMUTs, CMUTs, Piezocomposites
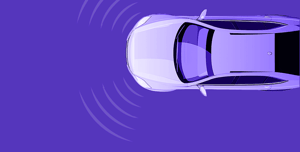
Automotive sensing
Parking sensors, passenger occupancy sensing
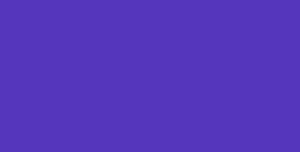
Underwater sonar
Piezocomposites, Piezo stacks (Tonpilz, Langevin)
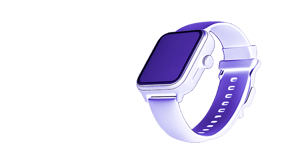
Wearable devices
Gyroscopes, accelerometers
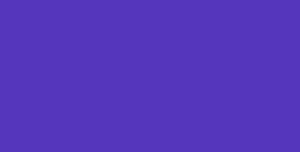
Microvalves
Electrostatic, piezoelectric, thermal microactuators
Estimating yield with a 1000-simulation Monte Carlo analysis
Even small variations can cause significant differences between what we expect in theory and how the device performs in real life.
Through a Monte Carlo analysis you can simulate these variations to predict their impact on device performance.
This method is particularly valuable as it allows engineers to estimate manufacturing yield using pass/fail criteria.
In our webinar in June, we covered the application of Monte Carlo analysis with a single-element PMUT model, running 1000 random variations to analyze performance effects.
This approach ensures greater reliability and efficiency in MEMS design, bridging the gap between simulation and real-world performance while significantly improving manufacturability and yield estimation.
Watch this case example step-by-step →
Download the PDF summary ->
Total simulations | 1000 |
Amplitude fails | 252 |
Arrival time fails | 135 |
Total fails | 281 |
Yield | 71,9% |
Complete features for a comprehensive simulation workflow
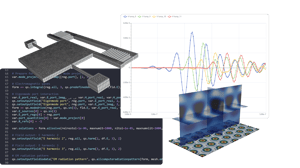
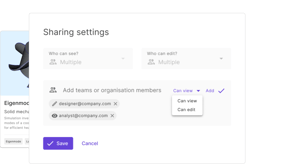
Unlimited users within an organization. Secure project sharing with custom permissions. No version incompatibilites.
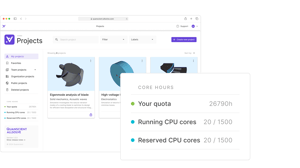
Flexible pricing according to capacity requirements. Access to high-performance computing resources without the overhead costs. Unlimited users with every plan.
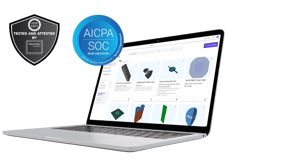
End-to-end data encryption. Strict access control protocols. Regular security audits (SOC2 & ISO 27001).
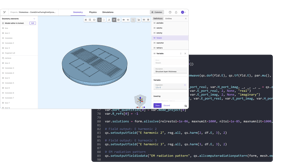
Intuitive and modern GUI. Python scripting interface for full control and customization. Pre-built script libraries.
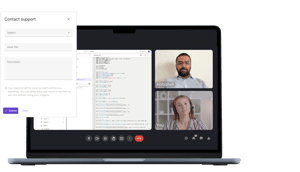
Comprehensive documentation and user guides. Support accessible directly in the platform. Expert support from our application engineers.
Learn more from these resources
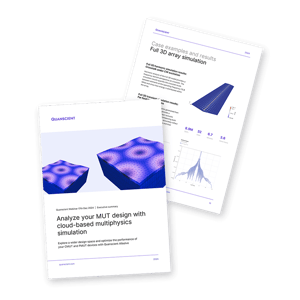
Webinar PDF summary
Analyze your MUT design with cloud-based multiphysics simulation
Blog
Why there's never enough simulation in R&D – and the next best thing
Webinar PDF summary
Faster and more reliable MEMS design with cloud-based multiphysics simulations
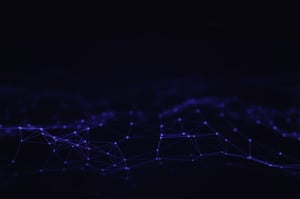
Try it out yourself
Submit the form to talk about a trial with our experts—we'll respond within 1 business day. With a trial, you'll have the ability to
- Validate your use case using Allsolve's full simulation capabilities
- Explore what's possible with scalable, cloud-native multiphysics simulation
- Get tailored support and insights from our team
Interested in just learning more? Schedule a 30-minute call here