Advancing fusion energy development with Quanscient Allsolve
Allsolve is a key tool for us modelling HTS cables and coils, especially when dealing with complex 3D multiphysics simulations. It has significantly enhanced our efficiency.
About UKAEA
How Quancient Allsolve helped UKAEA
A key aspect of this project involves designing magnets using high-temperature superconductors (HTS), which are essential for creating a compact and efficient magnetic confinement system. This presents significant engineering challenges that demand advanced simulation capabilities to model the complex behavior of these superconductors.
UKAEA's magnet team, composed of engineers Jiabin Yang, Moray Arbuckle, and Funke Dacosta-Salu, is tackling these challenges with the help of Quanscient Allsolve. Their work focuses on developing intricate multiphysics simulations for the TF magnet and its fundamental component, the HTS cable.
These simulations include a wide range of phenomena, including critical current prediction, AC losses, quench propagation, and thermohydraulic flow in cooling channels. The team also investigates the quench behavior of the entire TF magnet under various operational scenarios.
Challenges in simulation before Quanscient Allsolve
Before adopting Quanscient Allsolve, the UKAEA magnet team faced several obstacles in their simulation and design processes.
Hardware limitations were a major concern, as the memory and processing power of their remote workstations proved insufficient for the demanding simulations required for their research.
Furthermore, the team's efficiency was hindered by restrictive licensing agreements of commercial software, which often limited usage to a single user at a time.
Finally, the team found it challenging to perform cross-validation between different simulation tools due to a lack of accurate and specialized tools for HTS simulation.
These limitations highlighted the need for a more powerful and flexible simulation platform.
Discovering and adopting Quanscient Allsolve
UKAEA's journey with Quanscient Allsolve began with an introductory meeting where Jiabin Yang, leveraging his expertise in HTS modeling, recognized the potential of Allsolve's approach to simulation.
To gain a comprehensive understanding of the software, he organized a product demonstration and a workshop for the UKAEA magnet team. He further explored Allsolve's capabilities by reading research papers published by Quanscient and examining demo videos.
A key factor that drew his attention was the alignment of Allsolve's research focus with UKAEA's specific needs, particularly in collaborative studies conducted with other players in the fusion energy sector.
The availability of the H-phi formulation, tailored especially for HTS simulations, further solidified their decision to start adopting Quanscient Allsolve.
Allsolve’s primary advantages are its ability to rapidly simulate large-scale magnets and its script interface, which allows flexible handling of physical parameters and equations.
Initial impressions and first benefits
As the UKAEA team started their work with Quanscient Allsolve, they encountered the typical learning curve associated with any new software platform. However, they quickly recognized the inherent advantages Allsolve offered.
The ability for multiple team members to collaborate simultaneously on the same model, coupled with access to extensive hardware resources through Allsolve's cloud-based infrastructure, significantly improved their efficiency.
As they gained proficiency with the software, they quickly learned to leverage scripting capabilities to automate tasks and introduce greater flexibility into their workflow.
Challenge | Before Allsolve | After Allsolve |
---|---|---|
Computing power | Limited by the computing power of local workstations | Access to cloud computing resources with extensive memory and parallel processing enabling large scale 3D simulations |
Collaboration | Single-user licenses hindered team efficiency | Flexible licensing allowing for collaborative model editing and increased efficiency |
Model set-up | The need for manual definition of the thin cuts for complex coil geometries unnecessarily increased model complexity | Automatized thick cut generation makes model set-up and meshing simple |
Total voltage | Simulation tool lacked direct access to the total voltage | Allsolve's H-phi formulation directly incorporates the total voltage, enabling more accurate design optimization |
Support | Limited support resources | Faster and more thorough responses through a proactive and knowledgeable support team |
Allsolve's impact on TF coil quench simulations
One project where Allsolve made a significant impact was in the simulation of quench events in UKAEA's partially insulated Toroidal Field (TF) coils.
These coils, with dimensions reaching 10m x 20m, require full 3D multiphysics modeling to accurately simulate quench behavior. Allsolve provided several key advantages for this challenging task:
- High-performance computing: The demanding computational requirements of these simulations were met by Allsolve's cloud-based hardware, offering access to terabytes of memory and massive parallel processing capabilities. This eliminated the limitations of local workstations and allowed for efficient simulation of large-scale models.
- Simplified model set-up with H-phi formulation: Allsolve's H-phi formulation streamlined the simulation setup by eliminating the need for introducing magnetic scalar potential discontinuities (thin cuts) manually via additional surfaces. In Allsolve, the automatic thick cut generation makes the simulation model set-up and geometry meshing simple for the user. Furthermore, this approach enables precise simulation of leakage currents within the partial insulation of a complex TF coil.
- Direct access to the total voltage: The H-phi formulation also provided a direct access to the total voltage as a dual quantity of the applied electric current. This is a crucial aspect for designing magnet protection.
Through these capabilities, Allsolve enabled UKAEA to rapidly iterate on their TF coil design, optimizing its performance and ensuring its safe operation under various quench scenarios.
Responsive customer support
UKAEA has been consistently impressed with Quanscient's customer support.
The support team has been proactive and helpful from the start, scheduling regular meetings and providing prompt responses to questions. This high level of support has remained consistent, even with changes in support team personnel.
UKAEA particularly appreciates the team's expertise and responsiveness to their needs. When they encountered a time-consuming issue related to importing external mesh data, the support team quickly developed and implemented a new feature to streamline the process.
This commitment to addressing user feedback and continuously improving the platform has been a valuable aspect of their experience with Allsolve.
Recommendations and future plans
UKAEA recommends Allsolve to others in the field. Its exceptional performance in simulating large-scale superconducting magnets, coupled with its ongoing development, makes Quanscient Allsolve a powerful tool for advanced high-temperature superconductor simulations for fusion energy.
In the near term, Allsolve will serve as the primary tool for 3D multiphysics simulations of TF magnets constructed from HTS cables within the UKAEA STEP program, particularly for quench protection concepts based on partial insulation.
Looking ahead, UKAEA envisions extending Allsolve's application to a broader range of fusion magnets and tokamak devices.
Success stories with engineers working on the most demanding engineering challenges
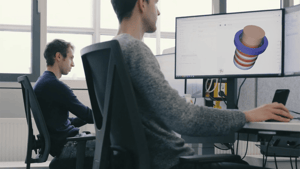
Allsolve made prototyping more reliable and helped us speed up development cycles.
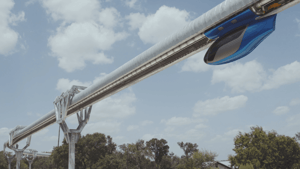
Simulation time down from 3 weeks to 8 hours with increased accuracy.
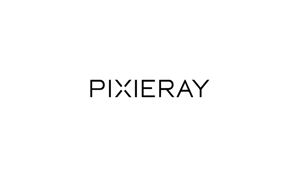
We were able to test different parameters to find the working design, saving three months in product development time.
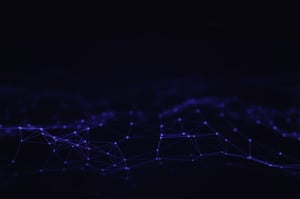
Request a live demo
In the live demo, we'll
- Explore use cases and workflow integration
- Discuss pricing and value
- Discover features and benefits
We'll get back to you within 1 business day.