About our guest author
Dr. Andrew Tweedie is the Founder and CEO of Kogsys, a consultancy specializing in ultrasound technology solutions. He has over two decades of experience in engineering, R&D, and startups, previously co-founding OnScale, a cloud-based engineering simulation platform.
I’ve spent most of my working life thinking about engineering simulation. How can we make it better? How can we give engineers more of what they need? What would the perfect simulation tool look like?
Talking to other engineers, there's a huge demand for this. There are bottlenecks in traditional simulation tools that slow down the design process and restrict ingenuity. So I definitely don’t feel alone.
From time to time, however, I hear comments like “I don’t need any more simulation capacity” or “I’m happy just running one simulation.” My response has always been “how can you say that!? I always need more, and I don’t see that changing any time soon”.
A harsh reaction perhaps, but let me explain…
The power of analytical models
Before working with numerical methods like the Finite Element Method (FEM) and Finite Difference (FD), I spent a lot of time using analytical models. At the time, my job was to design ultrasonic transducers, and there are some 1D analytical models which offer a great approximation of many simple designs. These models were quite primitive, but they ran in milliseconds, so they allowed me to simulate thousands of design variations very quickly. Running large design studies across multiple variables was trivial, provided I had the time to code up all the custom post-processing!
This quickly became fundamental to my design approach, which usually went something like this:
- Pick an initial starting design, which is either familiar from previous work, or at least makes intuitive sense.
- Carry out a design study around this point to discover how different parameters influence device performance.
- Discuss the results with colleagues and decide on the best path forward:
- Perhaps one of the designs that has been uncovered solves the problem.
- If not, perhaps we’ve gained some insight into the problem and can modify the design to access even better performance.
As well as providing a wealth of information on the design space, I’ve always felt like this approach represents the best teaching tool an engineer can access. It gives direct exposure to the cause-and-effect relationships that underpin the operation of the device under study. I’m a very hands-on learner, and I feel I’ve picked up more through this approach than simply studying literature.
The transition to FEM and the need for more
Fast forward a few years, and the devices we were working on became more complex, the designs more challenging. We didn’t have analytical models that were valid for the structures we were considering. We needed something more general, and FEM was the tool for the job. But imagine my reluctance to move to an approach where the sheer computational cost often means that only a handful of simulations are feasible in an entire project! I eventually gave in and started to work on ways that I could improve the FEM simulation experience. Since then, I think it’s fair to say that this has become my life’s work.
Cloud computing as a game-changer
For me, the real game-changer has been cloud computing. I’ve now been working on cloud-based engineering simulation for over 10 years. Cloud computing solves several of the traditional problems with FEM:
- It lets us run many simulations in parallel
- It removes hardware bottlenecks
- On some advanced platforms like Quanscient Allsolve, it allows us to accelerate large simulations across thousands of cores
- It removes the licensing restrictions common with traditional FEM packages
- It allows teams of engineers to collaborate on the same project. No more working on your own!
Allsolve is currently my go-to tool for FEM. It’s over 20 years since I ran my first ultrasonic transducer simulation using FEM, and Allsolve can do that job over 1,000x faster. It allows me to run large design studies over multiple variables. It allows me to conduct Monte Carlo analysis to look at a design’s robustness. In essence, it allows me to ask the big questions, explore and learn - all things that I believe a good engineer should be doing.
The quest for more
Is it “enough”? Honestly, I’ll always want as much simulation capacity as you give me. But it’s pretty close to what I’ve been pushing for a long, long time.
So when I hear engineers say that they don’t need more simulation, I always ask this: what would you do if you could run as many simulations as you want? Instantly? What would you explore? How would it improve your design’s performance, your time to market?
These are the questions engineers should ask, and as innovators in simulation, it’s our job to give them the tools to do it.
Join 1000+ others and start receiving our weekly blog posts to your inbox now
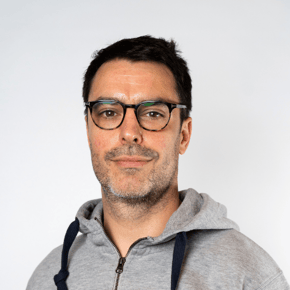