Expert contributor for this post
Dr. Mika Lyly
Senior Solutions Specialist at Quanscient
For over three decades, high-temperature superconductors (HTS) have been finding applications in industries, from energy and transportation to medical and scientific research.
These materials, capable of conducting electricity with zero resistance at relatively high temperatures, promise to enable more efficient, powerful, and compact technologies.
However, designing and optimizing HTS devices and systems is a complex task.
Simulations play a vital role in understanding the behavior of superconductors under different conditions, but traditional simulation tools often face limitations when dealing with the intricacies of HTS materials and applications.
These challenges include large-scale simulations demanding immense computational power and memory, complex geometries lacking symmetry which further complicate simulations, time-consuming transient simulations for dynamic behavior analysis, and the inability to perform extensive parameter sweeps for design optimization.
These limitations often lead to long simulation times, complex setups, and restricted design exploration, ultimately hindering the designs and delaying time-to-market.
Cloud-based multiphysics simulation offers a promising solution to these challenges.
By leveraging cloud computing, engineers and researchers are overcoming computational limitations, accelerating their design cycles, and exploring a wider range of design possibilities.
In this comprehensive guide, we’ll explore the current state of HTS simulation, the challenges faced by engineers, and how Quanscient Allsolve, a cloud-native multiphysics simulation platform, is helping engineers overcome these obstacles.
On-demand webinar
Accelerating fusion reactor design with cloud-based multiphysics simulations
Watch the full 60-minute recording and see how cloud computing and modern formulations enable more efficient stellarator and HTS magnet design.
Access recording and summary PDF ⟶
Overcoming bottlenecks in HTS simulation
Traditional simulation tools often encounter several bottlenecks when applied to the complexities of HTS systems, slowing down the design process:
-
Large-scale simulations
Simulating the behavior of HTS materials, especially in large-scale systems like fusion magnets or accelerator magnets, can require handling tens or even hundreds of millions of unknowns.
Traditional on-premise solutions often struggle to provide the necessary computational power and memory to handle such large-scale problems, leading to impractically long runtimes.
-
Complex geometries and lack of symmetry
Many HTS applications involve complex, non-planar coil geometries, such as those found in stellarators.
These intricate structures lack symmetry, making it challenging to simplify models or leverage symmetry for faster simulations.
Traditional tools often require extensive manual effort and expertise to handle such complexities, again, leading to longer simulation times and potential inaccuracies.
-
Time-consuming transient simulations
Accurately capturing the dynamic behavior of HTS systems under varying conditions, like AC currents or magnetic fields, often necessitates transient analysis.
These simulations are inherently computationally expensive, especially when dealing with non-linear materials and complex geometries.
Traditional software might require days or even weeks to complete such analyses, significantly slowing down the design process and limiting the exploration of different operating scenarios.
-
Extensive parameter sweeps
Design optimization, exploration of the parameter space, and AI training often necessitate extensive parameter sweeps, involving numerous simulations with varying inputs.
Traditional tools may struggle to efficiently handle these computationally demanding tasks, potentially limiting the ability to find optimal solutions and hindering innovation.
Evolutionary algorithm-based optimization methods, such as genetic algorithms or Grey Wolf optimization, further exacerbate this challenge by requiring the generation and simulation of large populations of designs.
With traditional tools, engineers are often forced to limit simulation times to mere tens of minutes to maintain practicality, potentially compromising the thoroughness of their optimization and exploration efforts.
These challenges highlight the need for a more powerful and efficient approach to HTS simulation.
Cloud-based solutions, with their virtually unlimited computational resources and other more advanced capabilities, offer a promising path forward for overcoming these bottlenecks and supporting the development of even more advanced HTS applications.
What cloud computing can do in HTS simulations
Quanscient Allsolve, a cloud-based multiphysics simulation software, addresses the challenges faced in HTS simulation by leveraging the power of cloud computing and advanced numerical techniques.
Cloud computing and the Domain Decomposition Method (DDM)
Allsolve's cloud-native architecture allows engineers to access virtually unlimited computational resources on demand.
This, combined with the Domain Decomposition Method (DDM), enables the efficient parallelization of large-scale simulations across multiple cores and nodes.
As a result, simulation times are significantly reduced, even for large and complex HTS geometries, enabling faster design iterations and more comprehensive exploration of the design space.
Model setup and post-processing
Quanscient Allsolve offers an intuitive graphical user interface (GUI) and a powerful Python scripting interface for streamlined simulation setups and advanced customization.
The GUI simplifies tasks like geometry creation, meshing, material property assignment, and physics definition.
It also automates aspects like generating cuts for unconstrained coils, enabling users to efficiently set up even complex multiphysics simulations.
Additionally, the Python scripting interface provides flexibility for advanced users, allowing them to reproduce and modify simulation setups, add custom physics not supported in the GUI, and leverage pre-built script libraries for faster development.
Allsolve's post-processing tools allow for in-depth analysis and visualization of results.
Users can calculate key parameters like AC losses, select and plot output fields, and better understand the electromagnetic and thermal behavior of their HTS designs.
The Thin-Shell method
In many HTS-applications, the aspect ratio between the smallest details and the perimeter of the design can be huge.
For example, in fusion magnets, a thin solder layer between the HTS-cable and the support structure can play an important role in the magnet dynamics. Moreover, the accurate modeling of the individual material layers of HTS tapes in a CORC-cable is required to further improve or optimize the design.
Especially in 3D simulations, including and meshing of thin layers can significantly increase the problem size and simulation times.
In the modeling domain, the so-called Thin-Shell method enables considering thin volume layers as surfaces [1]. This simplifies the geometry, makes the meshing easier, and reduces the problem size.
The thickness of the Thin-Shell can typically vary from micrometers to some hundreds of micrometers whereas the dimensions of the surrounding structures are in mm to m range.
Fig. 1 shows an example of the Thin-Shell method exploited in modeling an HTS-tape. The mesh and the norm of the magnetic flux density are shown in two cases: on the left the model with all the layers included, and on the right the model using the Thin-Shell method. [1]
[1] B. Alves, V. Lahtinen, M. Laforest, and F. Sirois, 2021, Thin-Shell Approach for Modeling Superconducting Tapes in the H-phi Finite-Element Formulation.
Watch a live example of the Thin-Shell method in our webinar!
See a live demonstration of the thinshell method, illustrating its ability to efficiently model thin layers in complex geometries and its application in stellarator multiphysics simulations.
Access recording and summary PDF ⟶
Modern cloud-based multiphysics simulation software is efficient at adapting to the quickly evolving field of HTS technology with new features and the full customization abilities provided by the Python scripting interface.
Furthermore, with automatic updates native to cloud-based solutions, engineers always have access to the latest features ensuring they are equipped to handle the latest HTS design challenges effectively.
Real-world applications
Quanscient Allsolve has been successfully applied to a wide range of HTS applications, including:
-
Large-scale simulations of nuclear fusion stellarators
Modeling complex magnetic field configurations and evaluating forces on superconducting coils.
-
Analysis of non-insulated 3D HTS coils
Simulating electromagnetic and thermal behavior of coils with complex geometries and current distributions.
-
AC loss calculations in superconducting wires
Accurately predicting energy losses in superconducting wires under AC conditions, crucial for optimizing their design and performance.
Case examples
Quanscient Allsolve has been successfully applied in real-world projects, helping engineers and researchers achieve results and overcome the limitations of traditional simulation software.
Large-scale nuclear fusion stellarator simulation
In a collaborative project with Proxima Fusion and Atled Engineering, Quanscient Allsolve was used to simulate a full-scale stellarator, a complex magnetic confinement device for nuclear fusion research.
The simulation involved over 300 million unknowns and required substantial computational resources.
Allsolve's cloud-based parallelization and DDM enabled the team to complete the simulation in less than 9 minutes using 500 cores, something that would have been impossible with traditional on-premise solutions.
This example demonstrates Allsolve's capability to handle large-scale, computationally demanding simulations in a fraction of the time, accelerating research and development in the field of fusion energy.
Non-insulated 3D HTS coil simulation
In our previous HTS webinar, we showed how Quanscient Allsolve can be used to simulate the magnetoquasistatic and thermal behavior of a non-insulated 3D HTS coil.
The simulation showcased the software's intuitive GUI and its ability to handle complex geometries and multiphysics interactions, including current sources, circuit coupling, and heat transfer.
Allsolve's automated features, such as automatic cuts for unconstrained coils, simplified the setup process and reduced the potential for errors.
The ability to efficiently and accurately simulate such complex systems allows engineers to optimize coil designs and improve their performance and reliability.
AC loss calculation in superconducting filaments
In this example, Quanscient Allsolve was used to run a simulation with five filaments embedded in a copper matrix using H-phi formulation.
With 1 399 033 degrees of freedom, the leading desktop multiphysics solver took 8 days to run it in a 96-core HPC.
Quanscient Allsolve solved it in just 1h 45 min using 640 cores. With just five cores, Quanscient Allsolve ran it in under 50 hours.
The results demonstrated Allsolve's capability to accurately predict AC losses, which is essential for optimizing the design and performance of superconducting wires for various applications, including superconducting motors and transformers.
These case studies demonstrate how Quanscient Allsolve is being used to solve real-world challenges in the field of HTS simulation.
Additional benefits of Quanscient Allsolve
Quanscient Allsolve offers a suite of features that enhance the HTS simulation workflow, beyond just the core capabilities.
-
Collaboration and workflows
Quanscient Allsolve promotes a collaborative environment by allowing unlimited users within an organization to access the platform.
This eliminates the constraints of traditional licensing models, enabling seamless teamwork and knowledge sharing.
Sharing projects is as easy as sharing a link, improving communication, and ensuring everyone stays on the same page.
The platform also ensures version compatibility, preventing delays and frustration due to incompatible file formats or software versions.
-
Costs and resource allocation
Allsolve's usage-based pricing model provides a flexible and cost-efficient alternative to the traditional upfront licensing fees.
This allows organizations of all sizes to access powerful simulation capabilities without large initial investments.
Additionally, the ability to scale resources up or down on demand ensures optimal performance and prevents overspending on idle capacity.
-
IT infrastructure and security
Quanscient Allsolve's cloud-native architecture eliminates the need for expensive hardware and complex software installations.
Accessible through any web browser, it simplifies IT infrastructure and reduces maintenance overhead.
Your sensitive simulation data is also safeguarded with Allsolve's cloud-based storage, leveraging advanced security measures and backups from industry-leading providers like AWS.
-
Features and updates
Keeping up with the quickly evolving HTS field requires access to the latest simulation capabilities.
Allsolve's automatic software updates ensure you're always working with the most up-to-date features, performance improvements, and bug fixes, allowing engineers to solve the latest HTS design challenges effectively.
-
Interface and customization capabilities
Allsolve offers both an intuitive graphical user interface (GUI) and a powerful Python scripting interface available for users with varying levels of expertise.
The GUI streamlines tasks like geometry creation, meshing, material property assignment, and physics definition, making it easy for even novice users to set up complex multiphysics simulations.
For advanced users, the Python scripting interface provides flexibility for reproducing and modifying simulation setups, adding custom physics not supported in the GUI, and leveraging pre-built script libraries for faster development.
These additional benefits, beyond core simulation capabilities, contribute to a more efficient, collaborative, and cost-effective HTS simulation workflow.
Quanscient Allsolve enables engineers to focus on innovation and design optimization, driving advancements in the field of HTS technology.
What experts say
The real-world impact of Quanscient Allsolve in addressing complex HTS simulations is evident in the feedback from engineers and researchers who have utilized the platform.
With Quanscient Allsolve, I can run complex simulations in under a day, which would otherwise take a week to complete.
Nicolo Riva, PhD
Magnet Engineer
Proxima Fusion
Quanscient Allsolve is a groundbreaking tool for advanced 3D superconductor simulations. They have proven to provide accurate results in a fraction of the time with their efficient scaling on cloud computing.
Antti Stenvall, PhD
Adjunct Professor
Tampere University
Quanscient Allsolve is the 'go-to' tool for our most sophisticated superconductor simulations in stellarator design.
Lucio M. Milanese, PhD
Co-founder and COO
Proxima Fusion
Conclusion
High-temperature superconductor (HTS) technology is advancing, but simulating and designing HTS systems remains challenging.
Quanscient Allsolve offers a solution to these challenges, enabling engineers and researchers to accelerate their work with HTS materials.
By leveraging cloud computing and advanced numerical techniques, Allsolve provides the necessary computational resources and flexibility to simulate complex HTS systems efficiently and accurately.
Real-world applications, such as nuclear fusion research and AC loss calculations, highlight its versatility. Allsolve's collaboration features, cost-effective pricing, and data security provide additional advantages.
If you missed the live webinar, here’s what you’ll find in the full 60-minute recording:
- How cloud computing can be utilized to efficiently simulate complex fusion reactors and handle large-scale simulations for intricate geometries
- How the thinshell method simplifies geometries while maintaining accuracy and reducing computational time
- The full workflow Proxima Fusion uses to automate their magneto-mechanical model integration with the Quanscient API
- Real-world results from Proxima Fusion, highlighting the value of advanced simulation tools in fusion research
Join 1000+ others and start receiving our weekly blog posts to your inbox now
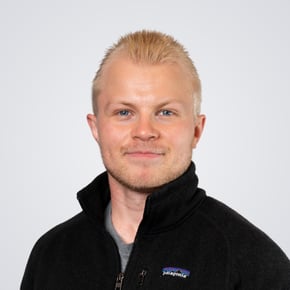