Designing MEMS devices presents a unique set of challenges for engineers because they involve multiple physical domains and often exhibit nonlinear behavior.
MEMS face ever-shortening product cycles, demanding rapid design optimization to ensure first-to-market advantage.
Maximizing yield is essential for profitability, and upfront consideration of manufacturing processes and real-world operating conditions can prevent costly delays and redesigns.
As such, high-end simulation plays a vital role in design optimization. However, traditional on-premise solutions inherently limit the size, complexity, and number of iterations that can be explored.
Licensing restrictions and hardware limitations act as an innovation bottleneck, restricting engineers from fully exploring new design possibilities in the fast-moving MEMS industry.
Fortunately, cloud-based simulation platforms are revolutionizing the way engineers approach MEMS design.
Through next-generation multiphysics solvers deployed seamlessly on the virtually unlimited resources of the cloud, engineers can optimize their designs significantly faster and more cost-effectively, while reducing risk and overall cycle times.
Webinar recording
Faster and more reliable MEMS design with cloud-based multiphysics simulations
Watch our on-demand webinar to see how engineers are leveraging cloud computing for faster design cycles and increased product reliability in MEMS design.
Along with the 60-minute recording, you will get access to a downloadable PDF summary of the webinar.
Access the webinar recording and PDF summary now
Common roadblocks in MEMS design
MEMS engineers face several challenges that traditional simulation tools can't fully address:
- Slow prototyping: Creating physical prototypes for each design variation is not only expensive but also introduces extended lead times. Extended lead times, in turn, not only delay product launch but also limit the ability to react quickly to manufacturing or reliability issues when they arise.
- Multiphysics complexity: MEMS often involve interactions between multiple physics domains (mechanical, thermal, electrical, fluidic). Simulating such interactions accurately and efficiently can be incredibly demanding for local computational resources. Simulating interactions accurately also necessitates considering packaging effects, which can significantly impact device performance.
- Limited design exploration: Due to time and cost constraints inherent to physical prototyping, engineers often find themselves unable to fully explore all potential design possibilities and reduce the chances of discovering a truly optimal design that maximizes yield and reliability.
- Meshing complex geometries: Creating accurate simulation meshes for the intricate details of ultrasonic sensor designs, for example, can be demanding, and limitations in local computing power can make it difficult to achieve the necessary level of detail.
How Quanscient Allsolve streamlines the design process
Quanscient Allsolve is the only multiphysics simulation software that allows engineers to address these challenges directly:
- Natively coupled multiphysics: Quanscient Allsolve provides the computational power needed to handle complex multiphysics simulations accurately with its strongly coupled multiphysics solver. Engineers can model the interaction between different physical domains in a single simulation, leading to a more comprehensive understanding of their MEMS design's performance.
- Faster iterations: Engineers can run complex multiphysics simulations in a fraction of the time compared to traditional on-premise solutions. This enables them to explore multiple design variants quickly and make data-driven adjustments without waiting weeks for prototype results.
- Scalable computational power: The cloud provides on-demand access to vast computational resources. With 100s of cores and terabytes of RAM instantly on-demand, engineers can run simulations that would otherwise be impossible on local machines, enabling the ability to capture fine geometric details and analyze transient behaviors with high accuracy.
- Optimized design exploration: With faster and scalable simulations, engineers can explore a wider range of design possibilities, leading to better optimization and ultimately, superior systematic performance of devices. Test thousands of variants of your design to find the optimal combination in a fraction of the time required by legacy tools.
- Manufacturing-aware design: Quanscient Allsolve enables you to incorporate fabrication constraints and explore material variations using Monte Carlo analysis. This ensures designs are robust and manufacturable from the start, reducing costly redesigns.
See a live demonstration of Quanscient Allsolve in our on-demand webinar
The key takeaways of the 60-minute webinar
- Gain a deeper understanding of the challenges in MEMS design and how cloud simulation offers solutions
- Learn how to utilize the power of cloud computing for increased design exploration through parallel simulations
- Discover strategies for optimizing MEMS designs for performance, reliability, and manufacturability
- See Quanscient Allsolve in action with a live demonstration of a microspeaker simulation, including setup, parameter sweeps, and results analysis
In addition to the webinar recording, you'll get access to the executive summary PDF.
Other benefits of a cloud-based solution
A cloud-based solution like Quanscient Allsolve offers advantages beyond addressing the core MEMS design challenges. These include:
No user limits
- Flexibility for teams: Any number of engineers, researchers, or collaborators can access Quanscient Allsolve within your chosen plan, facilitating seamless teamwork regardless of your organization's size.
- No barriers to access: Users don't need specialized hardware. The cloud-based nature of Allsolve means simulations can be set up and monitored from any device with a web browser.
- Easy sharing: Collaboration becomes as simple as sharing a link. Team members can work on simulations concurrently, review results, and provide feedback in real time.
Python scripting interface
- Automatically generated Python script: Allsolve automatically generates Python scripts that fully define your simulation setup.
- Extensibility for unique physics: If the GUI doesn't directly support certain physics, users familiar with FEM weak-form equations have the flexibility to add them using Python.
- Accessible knowledge base: The extensive multiphysics script libraries provide a valuable resource, offering pre-built simulation examples and templates to accelerate your work.
Usage-based pricing
- Predictable costs: Quanscient Allsolve's pricing is based on actual simulation runtime. You are not charged when simulations are idle, ensuring you only pay for the computational resources you use.
- Scalability for all: This model enables organizations of all sizes to access powerful simulation capabilities without large upfront investments in hardware and software licenses.
Support and materials
- Expert assistance: Directly contact Quanscient's simulation experts for technical support and guidance whenever you need it.
- Self-paced learning: Access a comprehensive library of resources, including tutorial videos, documentation, and user guides to quickly learn the software and expand your simulation expertise.
Conclusion
- MEMS design involves complex interactions between multiple physics domains, nonlinear behaviors, and demands rapid optimization to stay competitive.
- Traditional on-premise simulation tools often lack the computational power and flexibility to handle the complexity of MEMS design effectively.
- Cloud-based simulation platforms provide access to virtually unlimited resources, enabling faster simulations, more comprehensive multiphysics analysis, and wider design exploration.
- This translates to better-optimized MEMS designs that are robust, manufacturable, and offer superior performance.
- Cloud-based simulation solutions also offer improved collaboration, ease of access, and cost-effective usage-based pricing models.
Join our live webinar to see how engineers are leveraging cloud computing in MEMS design
Join our upcoming webinar to see how engineers are leveraging cloud computing for faster design cycles and increased product reliability in MEMS design
The 60-minute live event will be hosted on LinkedIn on June 18 10 am EDT / 3 pm BST.
Our technical speaker is the Team Lead of our Application Engineering Team, Dr. -Ing Abhishek Deshmukh.
Our special guest for the webinar is Dr. Andrew Tweedie, CEO of Kogsys, a consultancy specializing in MEMS design.
Dr. Tweedie has an extensive background in MEMS design and experience working with clients in the MEMS industry, helping them leverage Quanscient Allsolve to tackle design challenges.
He'll share practical examples of how Allsolve has accelerated development cycles, improved design optimization, and ultimately led to more reliable MEMS products. Dr. Tweedie will also be available to answer your questions during the live Q&A.
Access webinar recording and PDF summary now
Join 1000+ others and start receiving our weekly blog posts to your inbox now
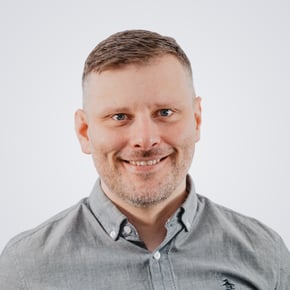