Expert contributors for this post
Dr. Abhishek Deshmukh & Rahul Nagaraja
Application Engineering Team
Key takeaways
- MEMS gyroscopes are small sensors used in consumer electronics, automotive systems, industrial automation, and more.
- Designing MEMS gyroscopes requires a deep understanding of multiphysics phenomena, including elastic wave propagation and fluid-structure interaction.
- Quanscient Allsolve's eigenfrequency analysis allows engineers to efficiently determine the natural frequencies and mode shapes of MEMS gyroscopes.
- With geometric sweeps and parallel simulations, Quanscient Allsolve enables extensive design space exploration.
Introduction
Microelectromechanical systems (MEMS) gyroscopes are incredibly small sensors that have become essential components in many consumer electronics, including smartphones, tablets, gaming controllers, and even drones. These tiny devices measure angular velocity, essentially detecting how fast an object is rotating and in what direction. This information is crucial for a wide range of applications, from the simple act of rotating your phone's screen to the complex task of stabilizing a drone's flight.
Designing a MEMS gyroscope that meets the demands of these diverse applications is a challenging task. Engineers need to consider various factors, including sensitivity (how accurately the gyroscope can detect rotation), energy consumption, size constraints, and manufacturing costs. One of the key challenges is to minimize energy loss within the gyroscope, which can arise from sources like viscous friction due to the surrounding air and energy dissipation through the anchors that hold the vibrating structure in place.
To address these challenges and optimize gyroscope performance, simulations play a vital role. By creating a virtual model of the gyroscope and simulating its behavior under different conditions, engineers can gain valuable insights into its performance and identify design modifications that can improve sensitivity, reduce energy loss, and ultimately enhance the overall functionality of the device.
In this blog post, we'll delve into the specifics of simulating MEMS gyroscopes using Quanscient Allsolve. We'll explore how Quanscient Allsolve's capabilities can help engineers overcome the challenges of MEMS gyroscope design and accelerate the development of high-performance sensors.
Why simulate MEMS gyroscopes?
As mentioned earlier, the sensitivity of a MEMS gyroscope is crucial for its accurate operation. Sensitivity refers to how effectively the gyroscope can detect and measure angular velocity. A highly sensitive gyroscope can detect even the slightest rotations, which is essential for applications like motion tracking and image stabilization.
One of the key factors influencing sensitivity is the separation between the frequencies of the gyroscope's driving and sensing modes. These modes refer to the specific ways in which the internal structure of the gyroscope vibrates. A good frequency separation ensures that the driving motion, which sets the gyroscope in motion, doesn't interfere with the sensing motion, which detects the actual rotation. This clear separation allows for more accurate measurements and reduces the impact of any imperfections or mismatches in the gyroscope's components.
However, achieving high sensitivity is not the only challenge in MEMS gyroscope design. Energy loss is another critical factor that can significantly affect performance. Two primary sources of energy loss are:
- Viscous friction: This occurs due to the interaction between the vibrating structure and the surrounding fluid, which is typically air. As the structure moves, it has to push against the air molecules, leading to energy dissipation. This effect is also known as squeeze-film damping.
- Anchor losses: The anchors that hold the gyroscope's vibrating structure in place can also contribute to energy loss. Vibrations can travel through the anchors into the surrounding substrate as elastic waves and dissipate energy.
The multiphysics nature of MEMS gyroscope simulations
Accurately simulating the behavior of a MEMS gyroscope isn't as simple as modeling a single physical phenomenon individually. Instead, it requires a multiphysics approach that considers the interplay between different physical processes happening simultaneously. In the case of a MEMS gyroscope, two primary physics come into play:
Elastic wave propagation: This refers to how vibrations travel through the solid structure of the gyroscope. Understanding these vibrations is crucial because they form the basis of the gyroscope's operation. When the gyroscope rotates, it induces Coriolis forces that cause the vibrating structure to deflect, and this deflection is measured to determine the rate of rotation. Simulating elastic wave propagation accurately is essential for predicting the gyroscope's sensitivity and response to different motions.
Fluid-structure interaction: This describes the complex interplay between the vibrating structure and the surrounding fluid (usually air). As the structure vibrates, it interacts with the air molecules, creating pressure waves and viscous forces that can dampen the vibrations and cause energy loss. This phenomenon, known as squeeze-film damping, can significantly impact the gyroscope's performance. Therefore, accurately capturing this fluid-structure interaction is crucial for realistic simulations.
To achieve accurate and reliable results, a multiphysics simulation must seamlessly couple these two physics. This means that the simulation needs to account for how the elastic waves in the structure influence the surrounding fluid and, conversely, how the fluid forces affect the structural vibrations. This coupling can be computationally challenging, but it's essential for capturing the true behavior of the MEMS gyroscope and making accurate predictions about its performance.
Quanscient Allsolve is designed to handle these multiphysics challenges. It provides a platform where engineers can seamlessly combine different physics and accurately simulate the complex interactions within a MEMS gyroscope. This capability enables more realistic simulations and better predictions of gyroscope behavior, leading to improved designs and faster development cycles.
Advantages of eigenfrequency analysis with Quanscient Allsolve
Simulating the behavior of MEMS gyroscopes requires a multiphysics approach that accounts for both the structural vibrations and the interaction with the surrounding fluid. This can be a computationally demanding task, especially when exploring a wide range of design parameters to find the optimal configuration.
Quanscient Allsolve offers a significant advantage in this regard with its dedicated eigenfrequency analysis capabilities. Eigenfrequency analysis is a technique used to determine the natural frequencies (or eigenfrequencies) at which a structure will vibrate. These frequencies are inherent properties of the structure and depend on its shape, material properties, and boundary conditions.
In the context of MEMS gyroscopes, identifying these eigenfrequencies is crucial for understanding their dynamic behavior and optimizing their performance. Traditionally, finding eigenfrequencies involves performing frequency sweeps, where the gyroscope's response is simulated across a range of frequencies. This can be a time-consuming process, especially for complex models.
Quanscient Allsolve's eigenfrequency analysis, however, provides a more direct and efficient approach. It directly calculates the eigenfrequencies, corresponding quality factors (Q) that quantify the damping in the system (higher the Q, better the frequency response), and corresponding mode shapes (the patterns of vibration) without the need for iterative frequency sweeps. This not only saves time but also provides more accurate and comprehensive information about the gyroscope's vibrational characteristics.
Furthermore, Quanscient Allsolve's eigenfrequency analysis seamlessly integrates with its multiphysics capabilities, allowing engineers to consider the coupled effects of structural mechanics and fluid dynamics in a single simulation. This integrated approach enables a more realistic and accurate prediction of the gyroscope's behavior, leading to better design decisions and faster development cycles.
By streamlining the eigenfrequency analysis process and providing a comprehensive multiphysics platform, Quanscient Allsolve enables engineers to explore a wider range of design possibilities, optimize critical parameters like frequency separation and Q-factors (energy loss), and ultimately develop higher-performing MEMS gyroscopes.
Case example
MEMS gyroscope simulation
Technical details of the simulations
To illustrate the capabilities of Quanscient Allsolve for MEMS gyroscope simulation, we conducted two distinct analyses focusing on different aspects of energy loss: anchor loss and squeeze film damping.
Results and visualization
The simulations conducted in Quanscient Allsolve provided valuable insights into the dynamic behavior and energy loss mechanisms of the MEMS gyroscope. The eigenfrequency analysis yielded detailed information about the natural frequencies and mode shapes of the gyroscope, considering the two different damping effects, one due to anchor losses and second due to the surrounding air.
Anchor losses
The drive mode and sense modes are depicted separately with corresponding frequencies and quality factors. The elastic wave propagation is visualized at the anchors within the substrate.
Drive mode | Freq: 38.8 kHz | Q-factor = 7.18834e+07
Sense mode | Freq: 46.2 kHz | Q-factor = 51262.4
Squeeze-film damping
For both drive and sense modes, the motion depicts the periodic displacement. The cut planes show the velocity and direction of the flow through the etch holes and other gaps.
Drive mode | Freq: 38.8 kHz | Q-factor = 429.17
Sense mode | Freq: 47.16 kHz | Q-factor = 105.10
The visualizations and data provide a clear picture of the gyroscope's vibrational characteristics and the influence of different energy loss mechanisms. These insights are crucial for guiding design decisions and optimizing the gyroscope's performance.
Geometric sweeps for design exploration
As the next step towards optimizing the design, an exploration of geometric parameters was performed. The width of the beam connected to the proof masses and the dimension of the square holes (etchdim) were varied independently and their effect on drive and sense mode frequencies were investigated as shown in the figure. The dimensions of the square holes affect the frequencies nonlinearly, while the width of the beam changes the frequencies in a linear way. Such design explorations provide the insights required to obtain an optimal design with a desired drive and sense mode frequencies and a clear separation between them.
Conclusion and key takeaways
The simulations presented in this blog post demonstrate the effectiveness of Quanscient Allsolve in analyzing the complex multiphysics phenomena that govern the behavior of MEMS gyroscopes. By leveraging Quanscient Allsolve's capabilities, engineers can gain valuable insights into the performance of these miniature sensors and optimize their design for specific applications.
Key takeaways from this analysis include:
- Seamless multiphysics simulation: Quanscient Allsolve allows for the seamless integration of different physics, enabling accurate simulation of the coupled elastic wave propagation and fluid-structure interaction that are essential for understanding MEMS gyroscope behavior.
- Efficient eigenfrequency analysis: Quanscient Alllsolve's dedicated eigenfrequency analysis capabilities provide a direct and efficient method for determining the natural frequencies and mode shapes of the gyroscope, eliminating the need for time-consuming frequency sweeps.
- Accelerated design exploration: The combination of efficient eigenfrequency analysis and comprehensive multiphysics simulation enables engineers to explore a wider range of design parameters and identify optimal configurations more quickly.
- Unlimited resources and fast runtimes: The cloud-based nature of Quanscient Allsolve provides access to virtually unlimited computational resources, allowing for fast and efficient simulations, even for complex models with millions of degrees of freedom.
- API support for workflow integration: Quanscient Allsolve's API enables seamless integration into existing design workflows, facilitating automation and the use of physics-based simulations for design of experiments (DoE), yield prediction, Monte Carlo analysis, and optimal design selection at the system level.
By providing a powerful and versatile platform for MEMS gyroscope simulation, Quanscient Allsolve enables engineers to overcome design challenges, accelerate development cycles, and ultimately create higher-performing sensors for a wide range of applications.
Visit our website to explore Quanscient Allsolve's features, read case studies, and schedule an introductory call. Our team of experts is ready to answer your questions and help you discover how Quanscient Allsolve can benefit your specific needs.
quanscient.com
Join 1000+ others and start receiving our weekly blog posts to your inbox now
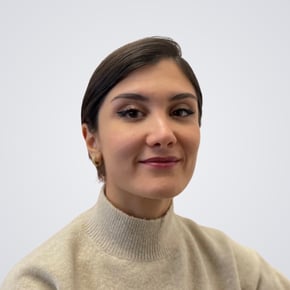