Expert contributor for this post
Rahul Nagaraja
Multiphysics FEM Software Developer at Quanscient
Key takeaways
- Semiconductor packaging design is becoming increasingly complex, demanding high-fidelity simulations to ensure performance and reliability.
- Traditional simulation methods struggle to handle the computational demands of modern, miniaturized packages.
- Cloud-based simulation offers a solution, providing the scalability and flexibility needed for efficient and comprehensive analysis.
- Quanscient Allsolve leverages cloud computing to accelerate simulations, enabling faster design cycles and optimized package performance.
- Allsolve provides advanced features like domain decomposition, parallel simulations, a Python scripting interface, and an API for automation and customization.
The microelectronics industry constantly pushes for smaller and more powerful devices. This miniaturization trend creates complex challenges for semiconductor packaging, demanding innovative solutions to ensure performance and reliability. Simulating these packages is crucial but presents difficulties.
Traditional simulation methods often rely on simplifying assumptions to manage computational costs and time. However, accurately capturing the behavior of modern, miniaturized packages requires detailed, high-resolution 3D models. This leads to significantly increased computational demands and longer simulation times, often exceeding the capacity of typical in-house resources.
These limitations restrict the scope of design exploration. Engineers need to perform extensive parametric studies and design of experiments (DOE) to optimize packaging designs. With traditional methods, these studies become time-consuming and resource-intensive, potentially delaying product development.
To address these challenges, a new approach to simulation is needed. Cloud-based solutions can offer the scalability and flexibility to handle the complex demands of modern semiconductor packaging design with cloud-native algorithms, enabling faster and more comprehensive analysis.
Challenges in semiconductor packaging simulation
As devices shrink and integrate more functionality, semiconductor packaging becomes increasingly complex. This complexity presents numerous challenges for traditional simulation methods:
-
Geometric complexity
Advanced packaging techniques often involve intricate designs and irregular geometries. This complexity limits the use of simplifying assumptions such as geometric symmetry and necessitates the use of full 3D models for accurate analysis.
-
High-resolution models
To capture the behavior of miniaturized components and fine-grained features, high-resolution meshes are essential. These detailed models significantly increase the number of elements and nodes in the simulation, leading to longer computation times and higher memory requirements.
-
Increased computational demands
Simulating complex geometries and high-resolution models requires significant computational resources. Traditional simulation tools may struggle to handle these demands, resulting in long runtimes that hinder design iteration and exploration.
-
Limited design space exploration
Thorough analysis of semiconductor packaging often involves extensive parametric studies and design of experiments (DoE). However, the computational cost of these studies can be prohibitive, limiting the ability to explore a wide design space and identify optimal solutions.
-
Resource constraints
Many engineering teams lack access to the high-performance computing (HPC) infrastructure needed for complex simulations. Procuring and maintaining such systems can be expensive and may not be feasible for all organizations.
These challenges emphasize the need for a more efficient and accessible approach to semiconductor packaging simulation. Cloud-based solutions, like Quanscient Allsolve, offer the scalability and flexibility to overcome these limitations and accelerate the design process.
Quanscient Allsolve
A cloud-based solution for semiconductor packaging simulation
Quanscient Allsolve addresses the challenges discussed in the previous section by leveraging the power and scalability of cloud computing. Here's how it provides a more efficient and accessible approach to semiconductor packaging simulation:
Domain Decomposition Method (DDM)
Allsolve utilizes DDM algorithms to accelerate simulations significantly. By dividing the computational domain into smaller subdomains and distributing the workload across multiple processors in the cloud, Allsolve reduces simulation runtimes. This parallelization approach enables engineers to obtain results faster, facilitating quicker design iterations and more extensive exploration.
Parallel simulations
Allsolve allows users to run multiple simulations concurrently. This capability is invaluable for performing parametric studies and design of experiments (DOE), where numerous design variations need to be evaluated. By running these simulations in parallel, Allsolve drastically reduces the overall time required for these studies, enabling engineers to explore a broader design space and optimize their designs more efficiently.
Cloud-based platform
Allsolve is a cloud-native platform, eliminating the need for expensive hardware investments and complex software installations. Users can access Allsolve from any location with an internet connection, scaling their computational resources as needed. This accessibility and flexibility make Allsolve a cost-effective and convenient solution for semiconductor packaging simulation, regardless of an organization's size or existing infrastructure.
By combining these features, Allsolve enables engineers to overcome the limitations of traditional simulation methods and accelerate the design process for semiconductor packaging.
Case example
IC Package Simulation
To demonstrate the practical benefits of Allsolve, let's examine a case study involving the simulation of a mock-up integrated circuit (IC) package. This example showcases how Allsolve's features contribute to faster and more efficient design analysis.
The model
The IC package model comprises an array of solder balls, a substrate layer, a routing track, a flip-chip ball grid array (FCBGA) with underfill, and an integrated heat spreader (IHS).
Mesh convergence study
A mesh convergence study was conducted to determine the appropriate mesh density for accurate simulation results. This involved running a series of simulations with progressively finer meshes, measuring the Z-displacement of a specific point on the substrate as a convergence criterion.
Reducing simulation runtime with DDM
To demonstrate the impact of Allsolve's DDM algorithm, simulations were performed with varying numbers of computational nodes. The results clearly show that increasing the number of nodes significantly reduces the simulation runtime. In this case study, using 60 nodes resulted in a runtime reduction of over 85% compared to a single node.
Parametric sweep for Design of Experiments
Allsolve's ability to run parallel simulations is particularly valuable for parametric studies and DOE. In this case study, a two-variable sweep was conducted, varying both temperature and the coefficient of thermal expansion (CTE). A total of 100 simulations were run in parallel, demonstrating a dramatic reduction in overall analysis time.
This case study demonstrates how Allsolve accelerates simulation workflows for IC packaging design. By leveraging DDM and parallel simulations, engineers can obtain accurate results faster, enabling more extensive design exploration and optimization.
Flexibility and automation with Allsolve
While speed is crucial, Allsolve offers more than just fast simulations. It provides a comprehensive and flexible environment for semiconductor packaging design, equipping engineers with advanced capabilities:
-
API for automation
For more advanced automation and integration needs, Allsolve offers an API enabling users to programmatically control simulations, integrate Allsolve with external tools and scripts, and build custom workflows. This allows engineers to automate repetitive tasks, connect Allsolve with optimization algorithms, or incorporate it into larger design automation systems.
-
Python scripting interface
Allsolve features a built-in Python scripting interface that provides direct access to the simulation setup. As you define your simulation through the GUI, Allsolve automatically generates a Python script that captures the entire configuration. This script can be accessed and modified within the Allsolve environment, allowing engineers to fine-tune parameters, add custom variables, or even incorporate their own physics equations. This provides a powerful way to customize and extend simulations without leaving the Allsolve platform.
-
Natively coupled multiphysics
Allsolve seamlessly integrates multiple physical phenomena within a single simulation environment. This enables engineers to analyze the complex interactions between structural mechanics, heat transfer, fluid flow, and electromagnetics. By considering these coupled effects, designers can gain a more complete understanding of package behavior and optimize performance across various physical domains.
-
User-friendly Interface
Allsolve features an intuitive graphical user interface (GUI) that simplifies simulation setup and analysis. The GUI provides clear visualizations, streamlines workflow management, and facilitates collaboration among team members. This user-friendly environment enables engineers to focus on their design objectives without being hindered by complex software interactions.
By combining speed, flexibility, and automation, Allsolve provides a comprehensive solution for semiconductor packaging simulation. It enables engineers to tackle complex design challenges, accelerate development cycles, and optimize product performance.
Conclusion and key takeaways
- The increasing complexity of semiconductor packaging, driven by miniaturization and advanced technologies, demands high-fidelity simulations to ensure performance and reliability. Traditional simulation methods often struggle to handle the computational demands of these intricate designs.
- Quanscient Allsolve leverages cloud computing to provide significant speed improvements and efficiency gains in the simulation process. By utilizing domain decomposition and parallel simulations, Allsolve accelerates analysis, enabling engineers to explore a wider design space and optimize package performance.
- Allsolve offers a Python scripting interface for customizing simulations and an API for integrating with external tools and automating workflows. This flexibility empowers engineers to tailor Allsolve to their specific needs and create powerful, customized design solutions.
- As a cloud-based platform, Allsolve is accessible to engineering teams of all sizes, eliminating the need for costly hardware investments. Its scalable architecture allows users to adjust computational resources on demand, ensuring they have the power necessary for their simulation tasks.
Visit our website to explore Allsolve's features, read case studies, and schedule an introductory call. Our team of experts is ready to answer your questions and help you discover how Allsolve can benefit your specific needs.
quanscient.com
Join 1000+ others and start receiving our weekly blog posts to your inbox now
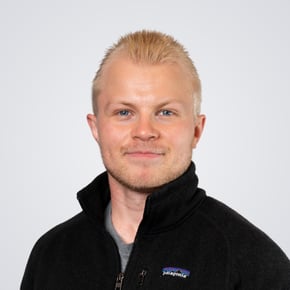