Technical authors
Dr. Mika Lyly
Senior Solutions Specialist
Dr. Janne Ruuskanen
Senior Solutions Specialist
Key takeaways
- Quench simulations in stellarator magnets are essential for ensuring safe operation and preventing damage to superconducting coils
- Quanscient Allsolve uses Domain Decomposition Method (DDM) to reduce computation time while maintaining accuracy
- Understanding quench behavior helps engineers improve protection strategies and coil design
- Quanscient Allsolve makes full-scale stellarator coil simulations feasible for fusion energy development
Introduction
Simulating quench events in stellarator fusion magnets is crucial to ensuring safe operation under different fault scenarios. These simulations provide valuable input parameters for designing effective quench protection strategies. Without an accurate understanding of how a magnet behaves during a quench, thermal and electrical instabilities could lead to severe operational risks, including permanent damage to superconducting coils or failure of the entire system.
Through this study, we aimed to address these concerns by leveraging high-fidelity numerical modeling to capture the complex interplay between electromagnetic and thermal phenomena in non-insulated (NI) windings. By predicting quench characteristics before real-world implementation, we enable the development of more reliable and resilient fusion energy technologies.
This project was conducted by Proxima Fusion in collaboration with Quanscient and Atled Engineering. The simulations were carried out by Quanscient and Atled Engineering.
Impact of Quanscient Allsolve on NI HTS stellarator coil analysis
One of the key challenges in modeling stellarator magnets is the enormous computational demand required to solve large-scale, highly detailed simulations. Traditional approaches struggle to efficiently process the vast number of unknowns involved in modeling superconducting windings, often leading to impractically long simulation times.
Quanscient Allsolve’s unique approach to DDM addresses this challenge by enabling large-scale simulations with over 40 million unknowns within a reasonable computational timeframe. By intelligently dividing the computational domain into smaller, manageable subdomains, DDM accelerates the solution process without sacrificing accuracy. This capability makes Quanscient Allsolve an invaluable tool for researchers and engineers working on next-generation fusion magnet designs.
Case example
Stellarator fusion magnet quench simulation
Simulation objective
The purpose of this simulation was to demonstrate the practical application of Quanscient Allsolve in modeling real-world high-temperature superconducting (HTS) stellarator coils. Specifically, we focused on a NI, non-planar double pancake coil designed for a stellarator reactor. This coil configuration is often favored for its direct current (DC) performance due to its ability to distribute current dynamically in response to changing conditions.
However, the complexity of NI HTS windings presents a unique challenge in accurately predicting their behavior, especially in the case of a quench event. A quench refers to the sudden transition of a superconductor from its superconducting state to a normal resistive state, which can lead to significant local energy dissipation and heat generation. Understanding quench characteristics is critical for designing safe and efficient fusion energy components.
By leveraging Quanscient Allsolve’s computational capabilities, we aimed to construct a high-fidelity model that could capture the quench dynamics, current redistribution, and temperature rise associated with a NI double pancake coil. The results of this study provide valuable insights into the feasibility of using finite element method (FEM) simulations, coupled with DDM, to analyze large-scale, real-size HTS magnet systems within a reasonable computational time.
The model
The stellarator coil we modeled consisted of a unit cell that included homogenized HTS stacks, copper, solder, and steel. A critical aspect of the coil’s structure was the insulation layer between the two pancakes, which allowed for controlled current flow while enabling bypass mechanisms typical of NI windings.
Fig 1: Stellarator coil geometry
Simulation model: Coupled magnetoquasistatic - thermodynamic
Analysis type: Transient
Model size: 42M Dof
Fig 2: DoF and core hour
Simulation process
To ensure the accuracy and efficiency of the model, we divided the simulation into three key steps:
- Ramp-up of current using linear material properties
This step accelerated the charge-up process by assuming linear resistivity for the materials involved. By doing so, we avoided excessive computation time while reaching a stable current distribution within the coil. - Transition to non-linear material properties
Once a steady-state current was established, the model transitioned to non-linear material properties to reflect real-world superconducting behavior. This step was necessary to establish a stable initial condition for quench simulation. - Quench initiation and controlled ramp-down of current
A localized defect was introduced within the coil to trigger a quench event. Once the quench was detected, the operation current was ramped down to analyze the current redistribution and the temperature evolution within the winding structure.
Key results
This case demonstrates that large, complex, and non-planar NI windings can be effectively simulated using FEM. Additionally, DDM has proven to be a highly efficient approach for reducing computation time while maintaining accuracy. These findings highlight the potential of FEM coupled with DDM as a practical tool for designing and optimizing real-size HTS NI magnets.
Key benefits demonstrated
Defect positioning
One of the most crucial aspects of quench modeling is understanding how defects within a coil structure influence the onset and propagation of quench events. In this simulation, the defect was strategically placed in the innermost turn of the coil. This positioning ensured that the quench was triggered effectively, allowing us to observe how the system responded to the loss of superconductivity in a localized region.
Fig 3: Defect
Magnetic field persistence
One of the most interesting findings of the simulation was that despite the ramp-down of the operating current, the magnetic field remained relatively constant initially. This persistence was attributed to the significant amount of energy stored within the coil’s magnetic field and current redistribution dynamics of a NI coil.
Fig 4: Defect and ramp down
Temperature rise and hotspot
Thermal analysis was a key focus of this study. The simulation showed a localized temperature increase, forming a distinct hotspot within the top pancake of the winding. The maximum temperature recorded in the winding reached approximately 170 K even though most of the energy was still stored in the coil’s magnetic field.
The ability to predict the magnets voltage and the hotspot temperature is critical for designing cooling systems and implementing early warning mechanisms for quench detection.
Fig 5: Temperature rise around defect
Quench dynamics
A key characteristic of NI windings is their ability to redistribute current dynamically among different turns of the coil. This behavior was clearly captured in the simulation.
As the quench progressed, the turns closest to the current leads experienced a decrease in current, while other turns picked up the excess current. This redistribution further propagated the quench, demonstrating the complex interplay between electrical and thermal factors in NI windings.
This result underscores the necessity of understanding NI behavior in large-scale magnet designs. The ability to model such interactions accurately can help optimize winding structures for better stability and performance.
Fig 6: Ramping down
Safety concerns
Perhaps one of the most important takeaways from this study was the safety implications of the observed quench behavior. The high temperatures recorded in the hotspot regions highlighted the potential for thermal damage if proper quench detection and mitigation strategies were not in place.
The results suggest that an effective quench detection system should be implemented to monitor real-time temperature changes and current redistribution patterns. Additionally, rapid ramp-down strategies need to be optimized to minimize thermal stress on the coil structure.
Other benefits of Quanscient Allsolve in stellarator coil simulations
Beyond the key insights gained from this particular study, Quanscient Allsolve provided several additional advantages that made the modeling process more efficient and practical for large-scale stellarator designs:
- Convenient model setup
Allsolve’s intuitive interface and built-in tools allowed for a streamlined setup process, significantly reducing the time required for pre-processing and initial modeling. - Automatic handling of unconstrained current loops
One of the challenges in simulating NI windings is dealing with unconstrained current paths. Quanscient Allsolve automatically handled these cases, ensuring that current redistribution was accurately captured without the need for extensive manual adjustments. - Direct access to total voltage of the magnet
The ability to directly measure and analyze the total voltage of the magnet provided valuable insights into the system’s response during quench events.
Conclusion
This study highlights the significant advantages of using transient models with built-in DDM for simulating large-scale, complex stellarator coils. The incorporation of DDM in FEM simulations allows for efficient computation times without compromising accuracy, making it a practical approach for tackling the challenges of modeling HTS NI coils.
One of the key takeaways from this work is the feasibility of simulating full-scale HTS NI stellarator coils within a reasonable timeframe. This capability is crucial for advancing nuclear fusion power plant designs, as it provides researchers with valuable insights into quench behavior and current redistribution in NI windings. By accurately capturing these dynamics, engineers can develop better quench detection strategies and optimize coil designs to improve stability and performance.
Furthermore, this simulation demonstrates the effectiveness of Quanscient Allsolve for predicting quench behavior in large HTS NI coils. The ability to model complex, real-size HTS magnets in a manageable time frame not only enhances research capabilities but also supports the practical development of next-generation fusion energy systems.
Collaborators
Join 1000+ others and start receiving our weekly blog posts to your inbox now
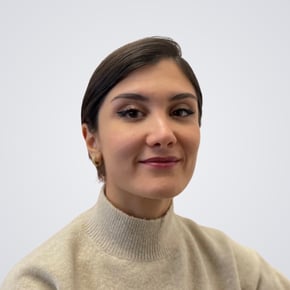