Key takeaways
- Micromachined Ultrasonic Transducers (MUTs) have significantly enhanced ultrasound imaging, making it more compact, portable, and accessible
- Designing high-performance MUT arrays remains challenging due to costly prototyping and limited simulation capabilities
- Traditional simulation tools struggle to simulate large-scale MUT arrays, hindering accurate predictions of real-world performance
- Quanscient Allsolve enables fully coupled multiphysics simulations of hundreds of MUT cells, allowing evaluation of key metrics like crosstalk and beam width
- With cloud-based parallel computing, Allsolve accelerates design studies, reducing the need for costly prototypes and enabling rapid design iteration
- Allsolve's capabilities, such as geometry and material property sweeps, help optimize MUT designs for various applications, supporting the development of next-generation ultrasound technology with improved efficiency and accuracy
Introduction
Micromachined Ultrasonic Transducers (MUTs) play a crucial role in advancing ultrasound technology, particularly in diagnostic ultrasound. These devices convert electrical signals into ultrasonic waves, which are used for imaging in various medical, industrial, and scientific applications. Over the years, MUTs have undergone significant improvements, making them a central component in modern ultrasound systems. They offer unique advantages, such as small size, high integration with control electronics, and low power consumption, which have made them increasingly viable for diverse uses.
One of the most notable achievements of MUT technology has been its impact on diagnostic ultrasound. Traditionally, ultrasound machines were bulky, requiring large rooms for installation. Today, thanks to advancements in MUT technology, diagnostic ultrasound systems have become more compact. Ultrasound imaging that once took place with machines the size of a refrigerator can now be performed using handheld devices, which can even stream their images to a mobile phone. This miniaturization has made ultrasound imaging more accessible, portable, and affordable, greatly improving patient care.
Despite these advances, engineers still face several challenges in the design and optimization of MUTs. Designing high-performance MUT arrays remains a complex and costly task, as prototypes are expensive to produce, with tapeouts typically costing upwards of six figures. The high cost of prototyping places significant pressure on engineers to get the design right on the first attempt, avoiding costly iterations.
Moreover, traditional simulation tools often fall short when it comes to simulating MUT arrays, especially those that consist of thousands of cells. These tools typically only allow for the simulation of a handful of MUT cells at a time, which is insufficient for accurately predicting the performance of larger arrays. As a result, engineers struggle to obtain realistic performance metrics, which can hinder the design and optimization process.
Impact of Quanscient Allsolve on MUT cell design and performance
Quanscient Allsolve provides a valuable solution to these challenges by enabling engineers to simulate much larger arrays of MUT cells. Allsolve offers fully coupled multiphysics simulations that can consider hundreds of MUT cells in an array. This capability allows engineers to evaluate critical array-level metrics such as crosstalk, beam width, and pulse shape, factors that directly influence the imaging capabilities of the ultrasound system.
Allsolve further enhances its value by providing the computational power necessary to conduct large-scale design studies. With the ability to run thousands of simulations in parallel, engineers can explore a wide range of design variations quickly and efficiently, significantly speeding up the design process. This large-scale simulation capability allows engineers to test multiple configurations and optimize their designs without the need for costly prototypes or multiple design iterations.
To demonstrate the power of Allsolve, consider the example shown in Fig 1. This figure presents a transient simulation of an array of 715 PMUT cells. A central linear element in the array is driven, and crosstalk is observed on adjacent elements. This type of simulation would be challenging or impossible to perform using traditional simulation tools that are limited to small-scale models. By enabling the simulation of large arrays in a fully coupled environment, Allsolve provides engineers with more accurate predictions of how their designs will perform in real-world conditions.
Fig. 1
Simple MUT cell example
Simulation objective
The first step in designing a high-performance MUT array is to design the individual MUT cell. This design must meet several key criteria, including the center frequency, bandwidth, and sensitivity. These factors are crucial in determining the overall performance of the MUT array, as they affect the quality of the ultrasound image produced.
In this section, we’ll explore how a compact model of a single PMUT (Piezocomposite Micromachined Ultrasonic Transducer) cell can be used to assess and optimize its performance quickly. The use of compact models allows engineers to conduct simulations more efficiently, saving both time and computational resources. In future articles, we’ll expand on how this analysis can be extended to consider the performance of the PMUT cell as part of an array, where the interactions between multiple cells can affect the overall performance.
The model
For this demonstration, we’ve constructed a model of the PMUT cell used in the paper by D. A. Horsley et al., titled “Ultrasonic fingerprint sensor based on a PMUT array bonded to CMOS circuitry,” presented at the 2016 IEEE International Ultrasonics Symposium. Originally designed as a fingerprint sensor, this device's core features make it suitable for use in ultrasonic imaging systems. For the purpose of this simulation, we are modeling the device operating in a water load, rather than in its original fingerprint-sensing application, to demonstrate its potential in general imaging scenarios.
In order to simulate the fundamental performance of the PMUT cell efficiently, we take advantage of symmetry in the system. This symmetry allows us to approximate the behavior of an entire array of PMUT cells by simulating just a single cell, effectively creating an "infinite" array that operates in unison. To reduce the size and computational complexity of the model, we simulate half of a cell. While this approach provides an efficient way to simulate the system, a quarter-cell model could also be used for even further optimization without compromising the accuracy of the results.
The overall device geometry is shown in Fig 2, while the geometry used for the simulation is depicted in Fig 3. dashed red lines depict planes of symmetry. The model setup closely replicates the key features of the PMUT cell, ensuring that the simulation results are representative of real-world behavior. The focus of this model is to understand how the PMUT cell would perform when immersed in a water load, which is typical for many ultrasonic applications, including diagnostic ultrasound.
For the simulation, we employ a transient solver to model the time-domain response of the PMUT cell to an applied voltage. This allows us to extract and analyze several key parameters that are crucial to understanding the device's behavior:
- Voltage and current: By simulating the voltage and current response of the PMUT cell, we gain insight into how the device behaves electrically. This is important for understanding the energy transfer process, the efficiency of the device, and the electrical characteristics that influence the performance of the PMUT cell in an array.
- Electrical impedance: Impedance plays a critical role in the overall system design. By analyzing the electrical impedance, we can determine how well the PMUT cell matches with the external circuitry, which is essential for ensuring maximum energy transfer and minimizing signal loss.
- Surface displacement: Surface displacement is a measure of how much the surface of the PMUT cell moves when the device is excited. This is a key mechanical parameter, as the displacement generates the ultrasound waves. By simulating the displacement, we can evaluate how the PMUT cell will behave in real-world applications.
- Acoustic pressure output: The acoustic pressure generated by the PMUT cell in the water load is a direct indicator of the effectiveness of the device in transmitting ultrasound waves. This parameter is vital for assessing how well the PMUT cell will perform as part of an ultrasonic imaging system.
To drive the simulation, a wavelet voltage pulse centered at a frequency of 16 MHz is applied to the PMUT cell. This pulse is chosen to mimic the typical operating frequencies used in diagnostic ultrasound applications. The transient solver calculates the cell’s response to this excitation over time, providing a detailed view of how the device behaves throughout the pulse duration.
Fig. 2 and 3
Key results
The results from the simulation provide valuable information regarding the performance of the PMUT cell. Some of the key results that can be extracted from the simulation include the voltage and current response of the PMUT cell, the electrical impedance, and the surface displacement. These factors are essential for understanding how the PMUT will interact with the surrounding environment and how efficiently it will convert electrical signals into ultrasonic waves.
Additionally, the acoustic pressure output is a critical metric for evaluating the performance of the PMUT in generating sound waves. By examining the acoustic pressure, engineers can assess how effectively the PMUT will produce the desired ultrasound signals for imaging.
Transmit sensitivity is another important parameter, as it determines how efficiently the PMUT cell can transmit energy into the water load, which ultimately impacts the quality of the ultrasound image.
Finally, an animation showing displacement in the device and acoustic pressure in the load is presented. This helps to give engineers a more intuitive feel for how the device is behaving.
Key benefits demonstrated
Quanscient Allsolve provides several key benefits that are particularly valuable in the context of MUT design. First and foremost, the ability to simulate large arrays of MUT cells in a fully coupled multiphysics environment enables engineers to more accurately predict the performance of their designs. This capability ensures that critical array-level metrics, such as crosstalk and beam width, can be evaluated early in the design process, which helps optimize the performance of the ultrasound system.
Additionally, Allsolve’s cloud computing capabilities enable large-scale design studies, allowing engineers to run thousands of simulations in parallel. This significantly accelerates the design process by making it possible to explore a wide range of design variations quickly and efficiently. Cloud computing also reduces the need for expensive physical prototypes, further driving down costs.
These additional features provide engineers with a robust toolset for optimizing MUT designs across a range of parameters.
Other benefits of Quanscient Allsolve for MUT cell design and performance
In addition to the benefits already discussed, Allsolve offers several other advantages for engineers working on MUT designs. One such benefit is the platform’s ability to handle geometry sweeps efficiently. Geometry sweeps involve varying the design parameters of the MUT cell to identify the optimal configuration for a given application. With Allsolve, engineers can quickly run multiple simulations with different design parameters, helping them find the best geometry for their specific needs.
Another valuable feature of Allsolve is its support for simulating different materials and loads. By simulating the interaction between the MUT cells and various materials, engineers can gain a deeper understanding of how their designs will perform in different real-world conditions. This feature is particularly useful for applications like medical imaging, where the properties of the tissue being imaged can vary significantly.
Conclusion
The development of high-performance MUT arrays is critical for advancing ultrasound technology, particularly in diagnostic ultrasound. However, engineers face significant challenges in designing and optimizing these arrays, from the high cost of prototyping to the limitations of traditional simulation tools. Quanscient Allsolve addresses these challenges by providing a comprehensive multiphysics simulation platform that allows engineers to simulate large arrays of MUT cells, evaluate critical performance metrics, and conduct large-scale design studies.
By enabling engineers to quickly and efficiently assess the performance of their designs, Allsolve helps to reduce design iteration costs and improve the overall quality of the final product. The ability to simulate hundreds or even thousands of MUT cells in a fully coupled environment is a game-changer for MUT design, allowing engineers to predict performance accurately and optimize their designs for real-world applications.
As the use of MUTs continues to grow in fields such as medical imaging and industrial ultrasound, Quanscient Allsolve will play an increasingly important role in the design and optimization of these devices. With its powerful simulation capabilities, Allsolve empowers engineers to innovate and improve ultrasound technology, making it more efficient, cost-effective, and accessible.
References
[1] Horsley, D. A., Lu, Y., Tang, H. Y., Jiang, X., Boser, B. E., Tsai, J. M., ... & Daneman, M. J. (2016, September). Ultrasonic fingerprint sensor based on a PMUT array bonded to CMOS circuitry. In 2016 IEEE International Ultrasonics Symposium (IUS) (pp. 1-4). IEEE.
Join 1000+ others and start receiving our weekly blog posts to your inbox now
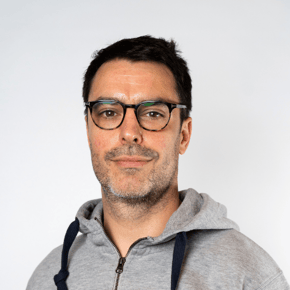